3D PRINTING RUBBER: THERMOPLASTIC POLYURETHANE’S MOST COMMON USES
Rubber is a familiar material known for its flexibility and toughness. It is often used for seals, vibration damping, and protective components, not to mention footwear and sporting goods.
At Materflow, we 3D print various parts and objects using thermoplastic polyurethane (TPU), a type of thermoplastic elastomer. TPU behaves much like traditional rubber, including flexibility, tensile strength, and wear resistance. This article introduces the most common uses of thermoplastic polyurethane.
TPU: EXTREMELY TOUGH AND FLEXIBLE
TPU is particularly flexible and tough, even compared to other rubbers, and it has excellent tensile strength, stretching up to 300% before breaking. TPU can be used to make very complex objects that still maintain their toughness and flexibility. Therefore, TPU is perfect for seals and protection. TPU also has excellent wear resistance and can withstand exposure to liquids, fats, and oils well.
Additionally, TPU is frequently used to create protective shells or covers for products made from other materials. For instance, it’s commonly used to produce resilient protective cases for electronics like tablets, providing a durable, flexible layer that enhances grip and protects the underlying device from damage. In such applications, TPU offers an effective solution for enhancing the longevity and usability of various parts and components.
COMMON INDUSTRIAL USES OF TPU
- Seals
- Vibration damping
- Grip plates
- Screen seals
- Tires
- Straps
- Plugs
- Various connectors
- Adapters for connecting different sized pipes
- Protective parts
- Hinge protectors
- Electrical connectors (insulators)
- Shoe soles, orthopedic applications, entire shoes.
TPU can also be used to dampen vibration in areas where, for example, an engine causes vibration, from which other parts should be protected. Various plugs, sleeves and adapters are also typical uses of TPU in manufacturing. Due to its flexibility, TPU effectively closes an end of a pipe, or connects two pipes of different sizes to each other in an airtight manner. Sometimes TPU is also used to replace silicone parts.
3D PRINTING TPU– WHY CHOOSE 3D PRINTING?
Both injection molding and vacuum casting are common techniques in TPU part production, each with distinct advantages depending on the nature of the application. Traditional manufacturing methods necessitate the use of molds, which involves a process that is not only costly but also time-intensive due to the required design and fabrication stages. Moreover, if any alterations are needed for the part, the mold must undergo a full overhaul, adding further to the time and cost.
With 3D printing, the production phase bypasses the need for mold manufacturing. All that is needed is a model of the part created with design software. If changes to the model are necessary, they can be made easily to the model file before the next batch is printed. 3D printing is thus particularly well suited for prototypes, when the details of the perfect part are still being tested and developed.
3D PRINTING LATTICE STRUCTURES – NEW OPPORTUNITIES FOR PROPERTY REGULATION
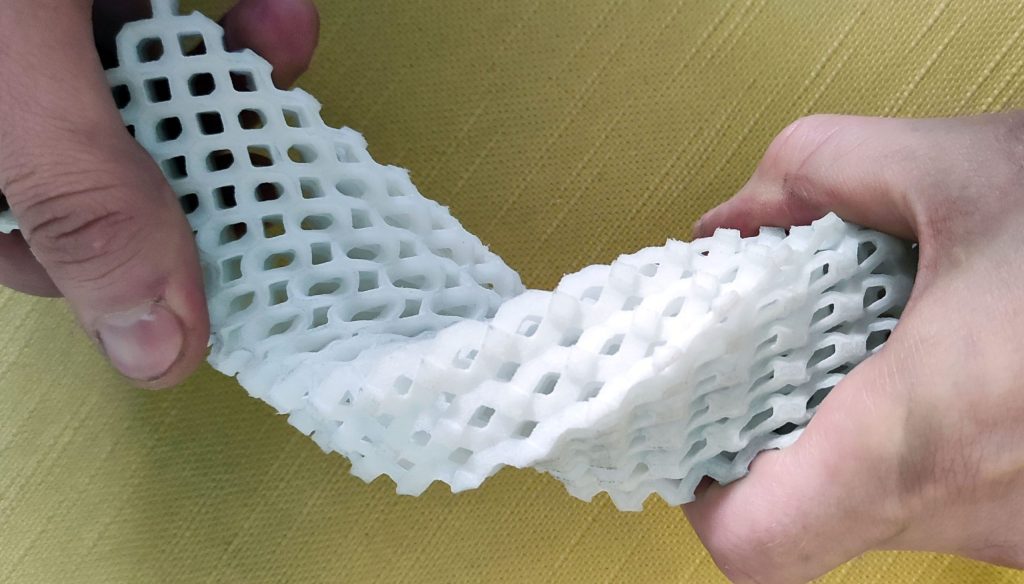
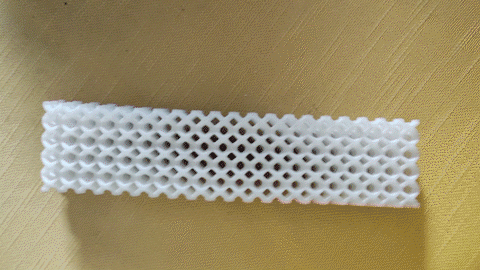
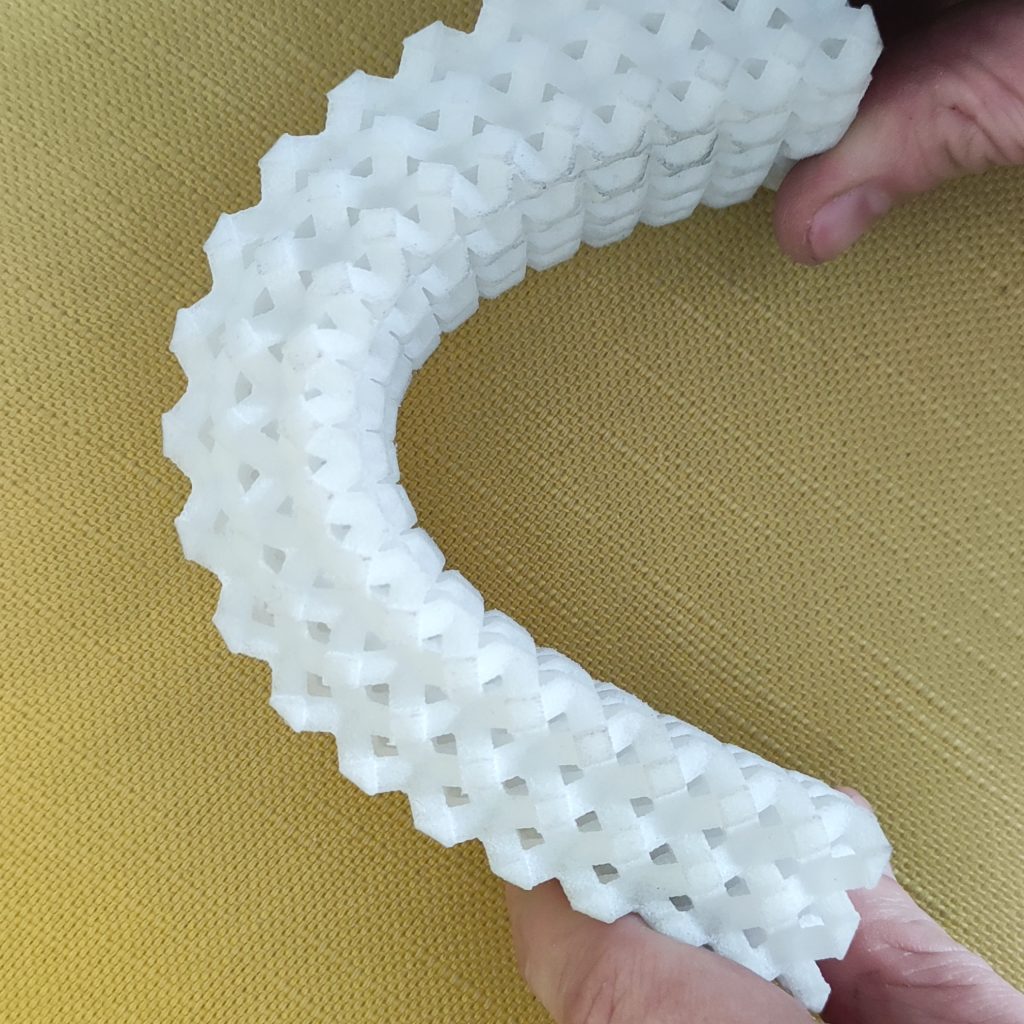
One of the revolutionary advantages of 3D printing is the ability to create intricate lattice structures that wouldn’t be possible with traditional manufacturing methods. Lattice structures are patterns that contain repeated cells or “lattices”, and they can be used to control the properties of the material, such as stiffness, durability, or flexibility.
When 3D printing TPU, lattice structures can precisely control the rubber-like material’s behavior. For instance, larger lattice structures can enhance the material’s flexibility, while denser or smaller lattices can make it stiffer. Using lattice structures can also reduce the weight of the material while maintaining its strength and durability.
Furthermore, the use of lattice structures can lead to cost savings and efficiency in the 3D printing process. Less material is needed, reducing raw material costs, and the printing time is shorter, increasing production efficiency.
This opens up new applications and design solutions in many industries. For example, car parts, sporting goods, and other applications can be precisely tailored for a specific purpose. By employing lattice structures, 3D printing provides an innovative tool for designing products that perfectly combine durability, lightweight characteristics, and flexibility.
Contact us and tell us about your project!
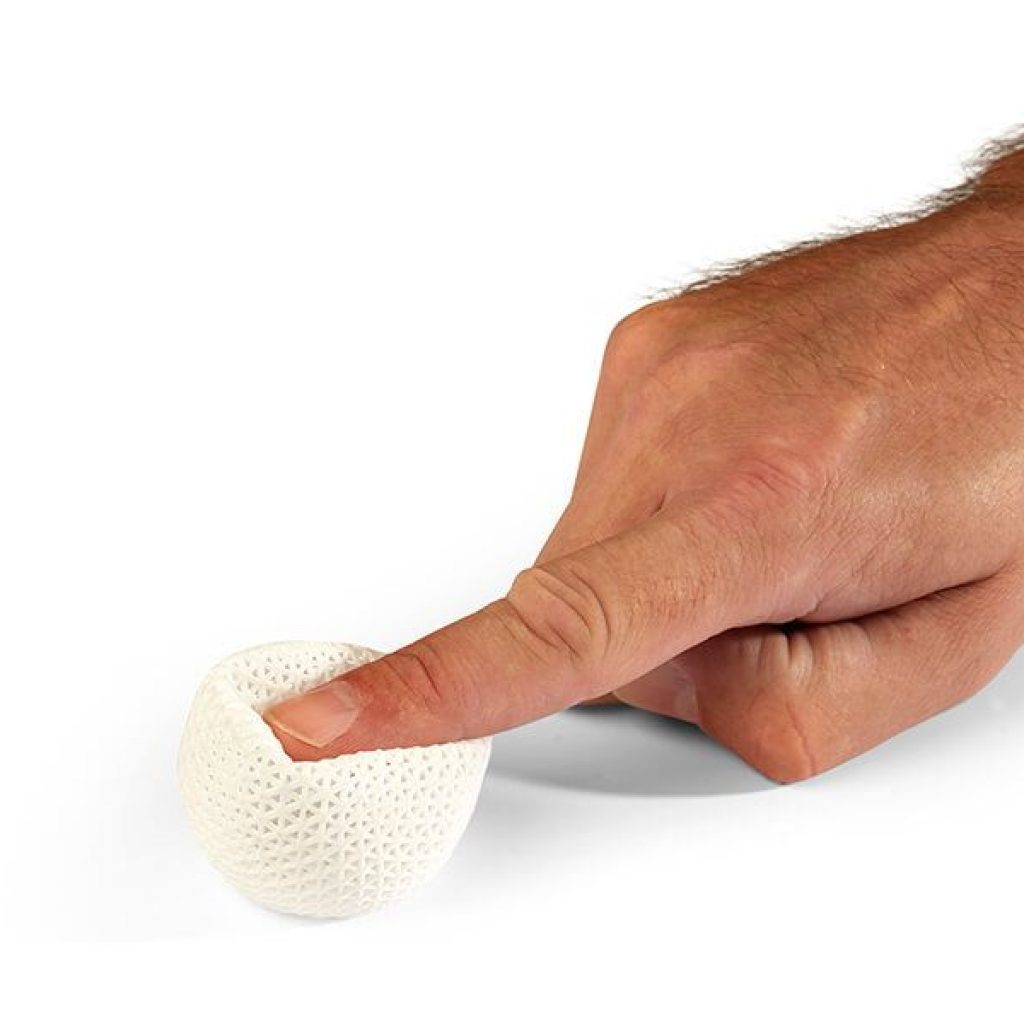
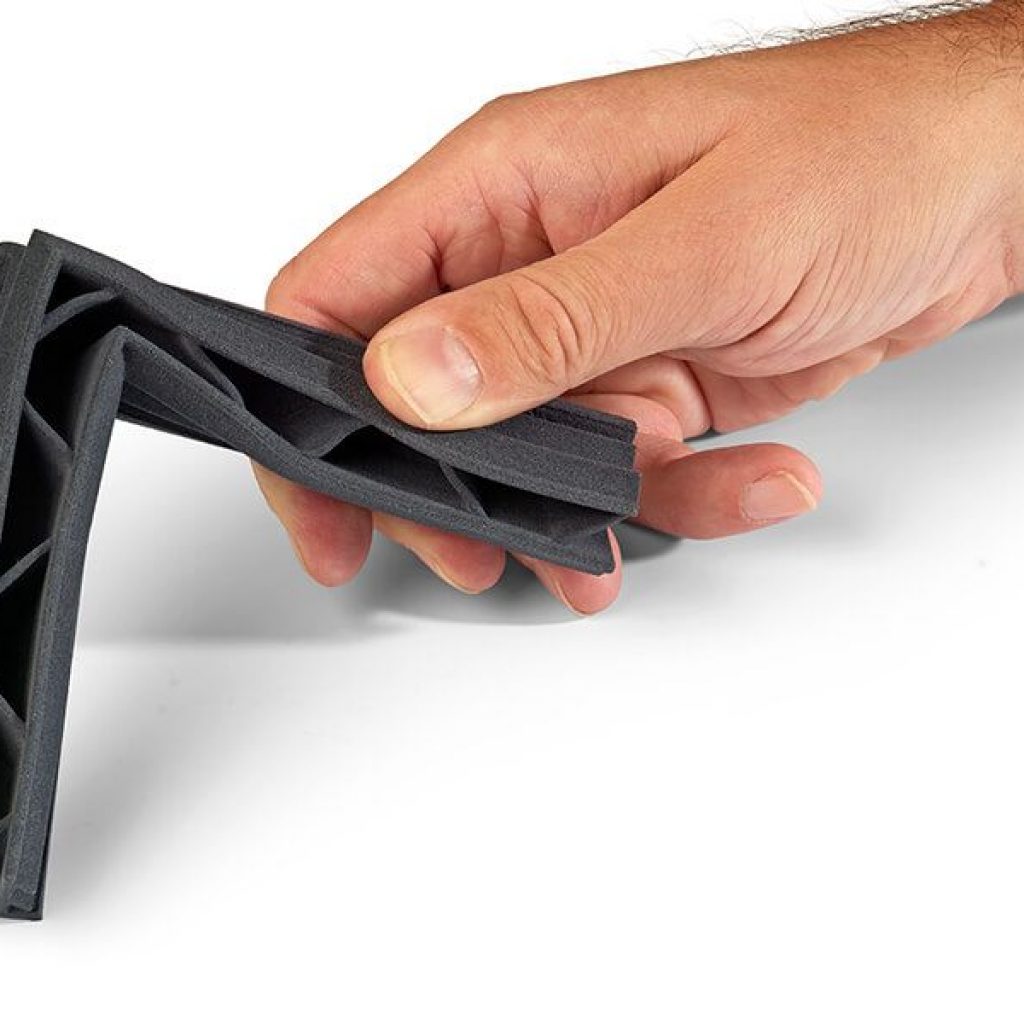
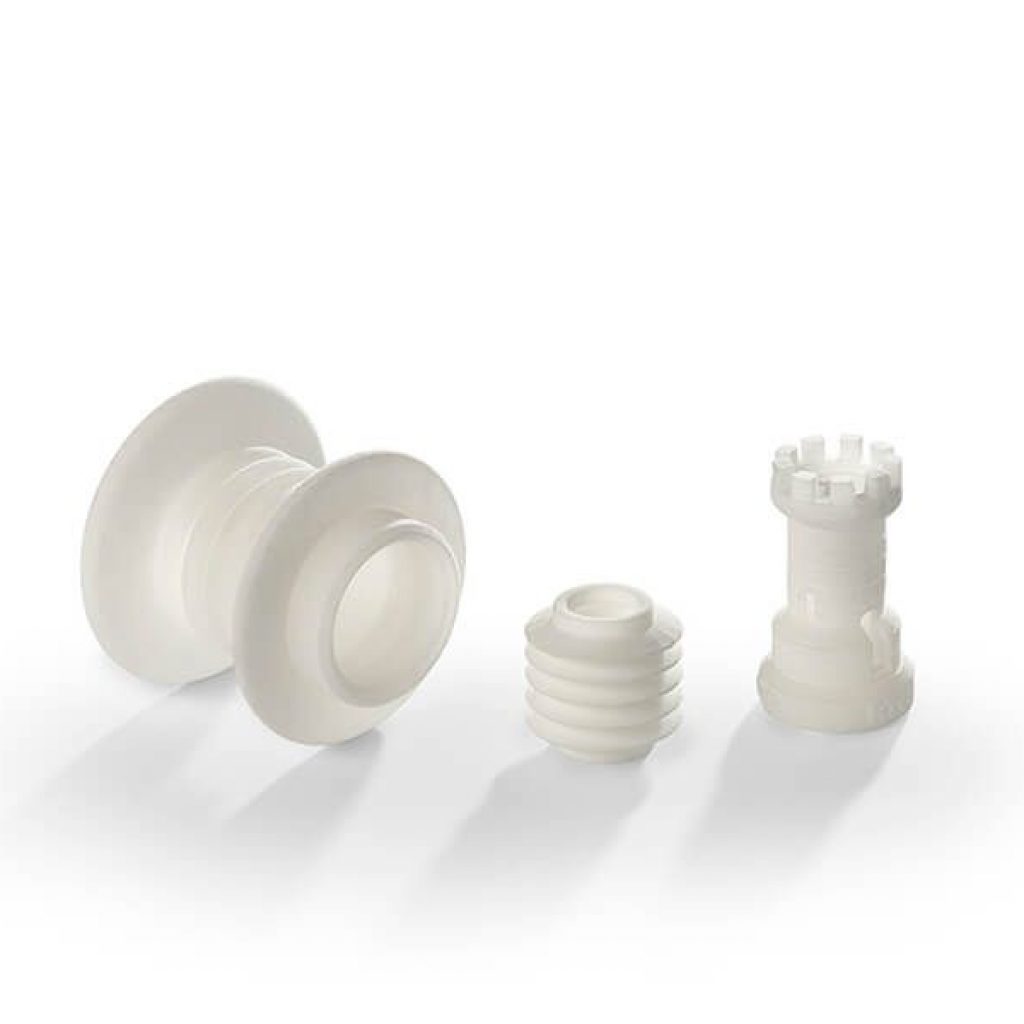